When we commit to upholding health and safety standards, it’s a collaboration between all stakeholders to do their part. An employer relies on the employee and vice versa. Any compromise in health and safety can mean downtime, injuries, liabilities, and sometimes worse. To anyone working in a setting that could be described as unsafe or that isn’t quite meeting standards, you need to make improvements.
The best way to improve health and safety is to prioritize it. Culture is set from the top down. Management should adopt a workplace safety culture that is reaffirmed and discussed with employees monthly or quarterly. Hear the concerns of those working alongside you. Make changes according to what you believe to be the root cause of these concerns or if you have seen an unfortunate injury.
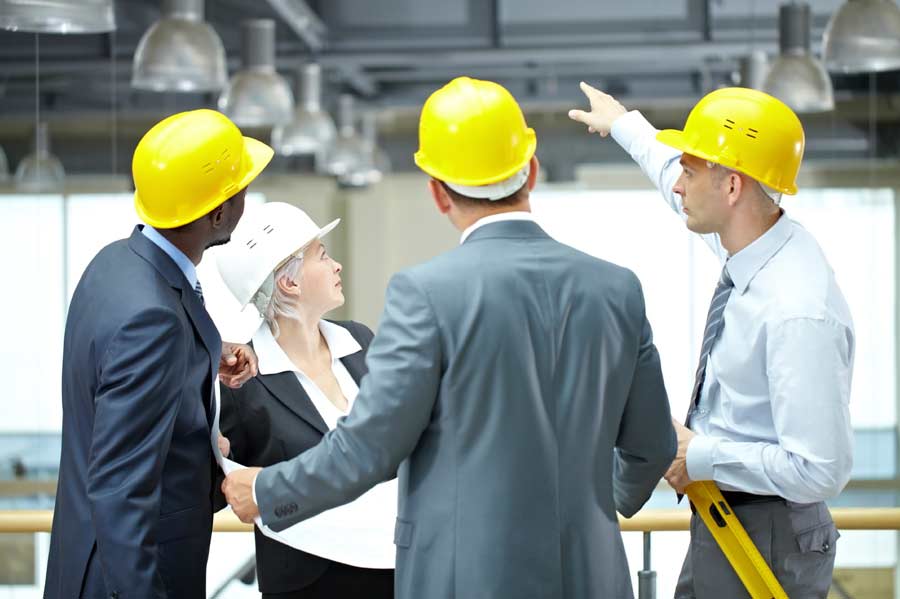
Be open to change. Make health and safety training an ongoing priority. This isn’t solved in a single day nor with a single set of directives. It requires constant monitoring and improvement. Here are a few steps towards how to improve the health and safety in the workplace.
Identify Hazards.
In every workplace, there are obvious hazards that can be identified with ease. Note them. Employees should be on alert when they are in situations with these hazards and understand expectations of conduct in these scenarios.
Signs should be used to identify hazards or clarify expectations around conduct in a given environment. This does not excuse the need to train the employee. What it does do is act as another reminder to those in these work settings to be aware of the hazards.
Develop Safe Processes.
For any sort of lifting, pushing, pulling, holding, carrying, or throwing, safe processes and equipment should be used to minimize the risk these movements put on the person doing them. Heavy machinery may be available to not only reduce safety risks, but also speed efficiency.
Some dangers are unavoidable. In those scenarios, every attempt to make the situation safer should be taken. This often involves using the right PPE or personal protective equipment, like masks, gloves, safety goggles, earmuffs, hard hats, earplugs, and whatever else may be appropriate for a task.
Assign a Health & Safety Rep.
A health and safety representative, or occupational health and safety expert, will be a way for employees to bring forth incidents and concerns, and get them handled quickly. A health and safety point-person can also identify hazards and make changes to the work environment to avoid injury. A manager may not always be able to see the same dangers a health and safety rep can.
Employees should not feel like they will be penalized for bringing to the attention of a supervisor health and safety hazards. Every employee should feel encouraged to tell a supervisor if they notice someone working unsafely, a compromised machine, or where there are increased hazards. Furthermore, no employee should be made to work in circumstances where they feel unsafe.
Adequate Employee Training.
Equip employees with the resources and reminders to know they’re performing their jobs safely, and implement an employee training plan to ensure that all bases are covered. This particularly applies in settings where workplace injuries are more common, so you must ensure employees have comprehensive safety training. They need to know the ins and outs of how to do their job without putting themselves or others at risk.
You should also train employees to use good posture. Injuries occur not only with hazards but through wear and tear on the body. Physical work relies on knowing how to hold the body up, how to lift things properly, and how to minimize the work your body goes through. Furthermore, if you’re working at a desk, you should still focus on maintaining an ergonomic posture.
Schedule Breaks Appropriately.
‘Burnout’ is real. It happens every day when employees are overworked. They grow less alert, work-related injury risk increases, and the safety of those around you also ends up compromised. This is why breaks should be scheduled at appropriate points throughout a shift to ensure employees are kept fresh for the day.
Sleep is essential to health and safety. Rest off the job promotes alertness on the job. For an employer, they can’t control what an employee does when they aren’t working a shift. That said, employees should be given enough days off to rest and be working shifts not unnecessarily long.
Maintenance & Cleanliness.
Do not take shortcuts in equipment maintenance. Tools and machinery that aren’t up to safety standards should not be used on the job. The misuse of a tool or using heavy equipment that’s compromised dramatically increases the likelihood of a workplace injury. Replace broken machinery. Fix what can be fixed. Ensure no equipment is compromised.
Similarly, injuries often occur due to a lack of cleanliness. A messy work environment is unacceptable. Ensure waste materials are safely contained, spills get cleaned, and floors are clear. Do checks throughout a shift, taking care of any disorganization as it happens. Even an experienced employee is put at risk when they’re working in cluttered settings.