As we look around and observe how technology is helping to manufacture, we can focus on the positive, but there is also a negative aspect of it all. For example, while lasers and robotics have enhanced manufacturing processes, they have also increased the potentials for danger. Parts wear out, and engineers are needed to repair them. The wiring needs to be replaced, and software has to be updated continuously to keep up with the demands. Machinery gets bigger to handle the larger workloads. As a result of larger workloads, machinery has to be shored up and protected so that the machinery isn’t harmed or broken. Technology is advancing manufacturing, but there is a price that has to be paid for superior efficiency and productivity.
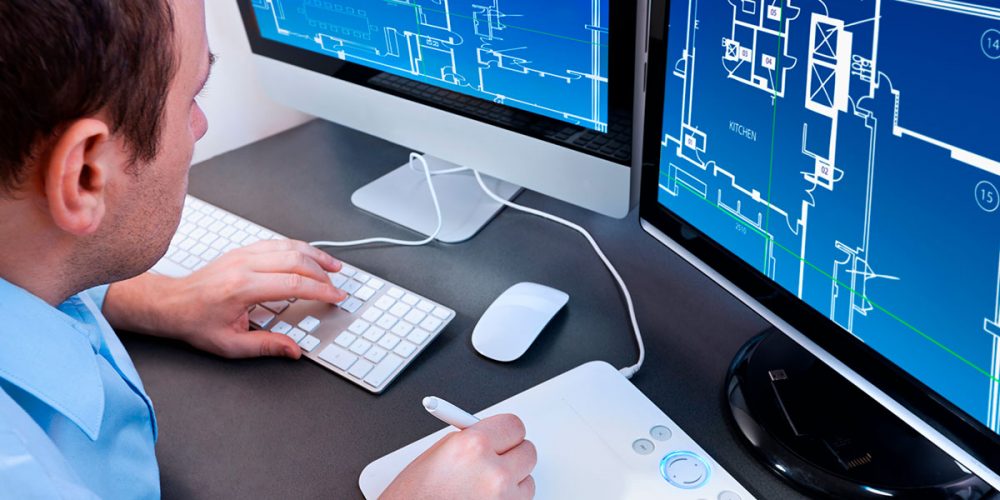
Wear Plate Technology
In today’s industrial manufacturing, “wear technology” is becoming more and more critical. The importance of wear technology comes from the constant use of wear plates that are needed on industrial machines. An industrial machine is always pulling heavy loads or making repetitive movements. The entire device is under pressure causing the machine to endure dense frictions. Abrasion wear plates are attached to the machinery to protect and extend the machine’s life. There are several companies that specialize in manufacturing technologies, like The A.J. Weller Corporation, whose technology is known throughout the industrial manufacturing world. The importance of wear technology in an industrial setting cannot be underestimated. Failing to have proper wear plates installed where they are needed could put human workers in harm’s way, break OSHA safety rules, and end in fines or revocation of licenses.
Saving on Costs
The use of wear plates not only saves on the industry’s wear and tear, but it also protects the overall costs of manufacturing. Wear technology saves the costs of producing the structures that are cut and welded by our lasers. Overall, wear technology is essential for production but also performs an added benefit to manufacturing. Machines can have prolonged usage because of the wear plates.
The bottom line is that the manufacturing industry needs to use wear plates for its safe operations as well as for keeping costs to a minimum. Money is saved when a company can extend the life of tools, machinery, and the equipment used to manufacture. Wear plates can be used in hopers, elevator shafts, in grain storage bins, and other intense friction bearing circumstances. Wear plates can be a handy addition to the production floor, where resistance is bound to flow, and the friction can cause the destruction of two materials rubbing together. Wear plate manufacturers use much of their revenue to research and develop better materials to produce more resilient wear plates.
Laser Technology in Manufacturing
Modern technology depends a great deal on laser technology. Lasers have revolutionized the way manufacturing operates. For example, one laser can do more than a thousand workers when operated efficiently. Laser technology is great for precision handling. Also, by using a laser, there is little need for human interference, unless there is an emergency. In industrial manufacturing, many patterns, blueprints, and molds have to be cut, welded and put together. With the correct lasers, an industrial manufacturing plant can feed all its blueprints into a computer that interprets the cutting designs for the laser. Once the designs are interpreted for the laser, all human interaction can walk away and proceed to other jobs. The human operator is only necessary for mechanical failures or system checks; otherwise, the laser machine can perform advanced operations unattended.
Uses of Lasers in Manufacturing
Lasers are used in four primary ways on the industrial production floor. First, there is a laser vaporization cutting. A vaporization cut by a laser heats the material very quickly and then produces the cut in the material. Laser melting performs the cutting by blowing away the liquid metal from the slab of steel after the non-oxidizing spray is applied to the metal. Laser oxygen cutting is similar to oxyacetylene cutting. Lastly, there is a laser scribing. Laser scribing scans the brittle steel heats it, and when pressure is applied along with the cut, the brittle material will fall where it has been cut. With the advent of laser technology, there has been a shift where lasers have been applied to 3D printing and modeling. Prices of these creative technologies are being driven down.